Pendahuluan
Ada berbagai istilah dalam menamai era sekarang ini. Jika dilihat dari teknik penulisan dan penyimpanan data, saat ini disebut era digital dimana data yang biasa disimpan secara fisik dan manual bermigrasi ke data digital. Data diprogram dengan bahasa pemrograman komputer sehingga efektif, efisien dan manageable. Jika dilihat dari dampak digitalisasi terhadap perubahan perilaku sosial berikut jenis pekerjaan yang berubah, era ini bisa disebut era disruptif. Era ini menunjukkan bahwa ada banyak “kekacauan” dan anti mainstream dari semua sistem kehidupan yang dianggap mapan pada masa masa lalu (Kasali, 2018). Jika dilihat dari variasi-variasi pekerjaan yang muncul di era disruptif, era ini disebut era Revolusi Industri 4.0.
Konsep Revolusi Industri 4.0 diperkenalkan pertama kali oleh Prof. Klaus Schwab, seorang Ekonom terkenal dunia yang berasal dari Jerman, pendiri dan ketua eksekutif World Economic Forum (WEF). Dalam bukunya yang berjudul “The Fourth Industrial Revolution”, Schwab (2017) menjelaskan bahwa Revolusi Industri 4.0 telah mengubah pola hidup dan kerja manusia secara fundamental. Berbeda dengan revolusi industri sebelumnya, revolusi industri generasi ke-4 ini memiliki skala, ruang lingkup dan kompleksitas yang lebih luas. Kemajuan teknologi baru yang mengintegrasikan dunia fisik, digital dan biologis telah mempengaruhi semua disiplin ilmu, baik di bidang ekonomi, industri, maupun pemerintahan. Bidang-bidang yang mengalami terobosoan berkat kemajuan teknologi baru di antaranya adalah robot kecerdasan buatan (artificial intelligence robotic), teknologi nano, bioteknologi, teknologi komputer kuantum, blockchain (seperti bitcoin), teknologi berbasis internet, dan printer 3D.
Revolusi Industri 4.0 merupakan fase keempat dari perjalanan sejarah revolusi industri yang dimulai pada abad ke-18. Revolusi industri 1.0 ditandai dengan penemuan mesin uap untuk mendukung mesin produksi, kereta api, dan kapal layar. Berbagai peralatan kerja yang semula bergantung pada tenaga manusia dan hewan kemudian digantikan dengan tenaga mesin uap. Revolusi Industri 1.0 memberikan dampak produksi dapat dilipatgandakan dan didistribusikan ke berbagai wilayah secara lebih masif. Namun demikian, Revolusi Industri 1.0 ini juga menimbulkan dampak negatif dalam bentuk pengangguran massal.
Revolusi Industri 2.0 dimulai pada awal abad ke-19. Revolusi Industri 2.0 ditandai dengan ditemukannnya energi listrik. Nama besar Tesla dan Edison mewarnai perkembangan revolusi industri tahap dua. Energi listrik mendorong para ilmuwan untuk menemukan berbagai teknologi lainnya seperti lampu, mesin telegraf, motor listrik, dan teknologi ban berjalan. Puncak dari Revolusi Industri 2.0 dalam bidang industri adalah diperoleh efesiensi produksi hingga 300 persen.
Perkembangan ilmu pengetahuan dan teknologi yang semakin pesat pada awal abad 20 telah melahirkan teknologi informasi dan proses produksi yang dikendalikan secara otomatis yang selanjutnya dikenal dengan Revolusi Industri 3.0. Mesin industri tidak lagi dikendalikan oleh tenaga manusia, tetapi menggunakan Programmable Logic Controller (PLC) atau sistem otomatisasi berbasis komputer. Dengan bantuan robot yang terpogram, Revolusi Industri 3.0 mampu mengotomatisasi sebagian besar proses produksi tanpa bantuan manusia. Dampaknya, proses produksi menjadi semakin cepat dengan hasil yang presisi dan biaya produksi yang semakin murah. Temuan tersebut cukup membawa perubahan yang signifikan pada pola hidup masyarakat. Revolusi industri mengalami puncaknya pada saat ini dengan lahirnya teknologi digital yang berdampak masif terhadap pola hidup manusia di seluruh dunia. Revolusi industri generasi keempat yang sering disebut Revolusi Industri 4.0, mendorong sistem otomatisasi di semua proses aktivitas. Lima teknologi sentral yang menjadi pondasi pengembangan Revolusi Industri 4.0, yaitu perangkat keras komputasi (computing hardware), perangkat keras produksi (production hardware), perangkat lunak (software),antar muka (interface), dan konektivitas dari empat aspek tersebut (Berger, 2016). Perangkat keras komputasi terdiri atas perangkat keras penyimpan data, sistem tertanam, komputasi berkinerja tinggi, komputasi dalam memori, antar muka sentuh/LCD, dan komputasi mikro. Perangkat keras produksi antara lain mencakup robotika, pencetakan 3D, mesin tradisional, dan peralatan otomasi. Antar muka meliputi sensor visual, pengenal frekuensi radio (Radio Frequency Identification, RFID), biometrik, pita magnetik, kamera dan sistem pencitraan, sensor semikonduktor, dan sensor tradisional. Perangkat lunak mencakup pemrosesan data waktu nyata, perangkat lunak proses bisnis, sistem manajemen basis data, komputasi awan, algoritma canggih, dan mesin belajar. Konektivitas yang menyatukan empat teknologi yang telah disebutkan sebelumnya melalui broadband bergerak dengan kecepatan tinggi (3G/4G/5G), internet industri, protokol internet (IPv6), broadband lokal (WIFI), dan transmisi jarak pendek/daya rendah (Bluetooth, Near-field Communication/NFC).
Gambar 1. Perjalanan Revolusi Industri (Jeevita and Ramya, 2019)
Revolusi Industri 4.0 membuka peluang yang luas bagi siapapun untuk maju. Teknologi informasi yang semakin mudah terakses hingga ke seluruh pelosok menyebabkan semua orang dapat terhubung di dalam sebuah jejaring sosial. Banjir informasi seperti yang diprediksikan Futurolog Alvin Tofler (1970) menjadi realitas di era Revolusi Industri 4.0 saat ini. Informasi yang sangat melimpah ini menyediakan manfaat yang sangat besar dalam dunia pendidikan terkait dengan penyiapan sumber daya manusia Indonesia yang handal.
Revolusi Industri 4.0 tidak hanya menyediakan peluang, tetapi juga tantangan bagi generasi milenial. Kemajuan ilmu pengetahuan dan teknologi sebagai pemicu Revolusi Indutri 4.0 juga diikuti dengan implikasi lain seperti pengangguran, kompetisi manusia vs mesin, dan tuntutan kompetensi yang semakin tinggi. Menurut Karnawati (2017), Revolusi Industri 4.0 dalam lima tahun mendatang akan menghapus 35 persen jenis pekerjaan dan bahkan pada 10 tahun yang akan datang jenis pekerjaan yang akan hilang bertambah menjadi 75 persen. Hal ini disebabkan pekerjaan yang diperankan oleh manusia setahap demi setahap digantikan dengan teknologi digitalisasi program. Dampaknya, proses produksi menjadi lebih cepat dikerjakan dan lebih mudah didistribusikan secara masif dengan keterlibatan manusia yang sangat minim. Di Amerika Serikat misalnya, dengan berkembangnya sistem online perbankan, telah memudahkan proses transaksi layanan perbankan. Akibatnya,
48.000 teller bank harus menghadapi pemutusan hubungan kerja karena alasan efisiensi (Sumber: https://regional.kompas.com/ read/2018/01/31/17225241/pekerjaan-yang-diprediksi-punah- akibat revolusi-industri-apa-saja). Bahkan menurut survei McKinsey, di Indonesia terdapat sebanyak 52,6 juta lapangan pekerjaan yang berpotensi digantikan dengan sistem digital (sumber:https:// public.tableau.com/profile/mckinsey.analytics#!/vizhome/ InternationalAutomation/WhereMachinesCanReplaceHumans). Namun demikian, bidang pekerjaan yang berkaitan dengan keahlian komputer, matematika, dan manufaktur akan semakin banyak dibutuhkan. Bidang-bidang keahlian ini diproyeksikan sesuai dengan tuntutan pekerjaan yang mengandalkan teknologi digital. Adapun skill industri di masa depan yang harus dikuasai oleh generasi millenial meliputi: complex problem solving, social skill, process skill, system skill, dan cognitive abilities. Rincian dari masing- masing skill industri tersebut dapat dapat dilihat pada Gambar 2.
Gambar 2. Skill Industri Masa Depan
Tantangan yang harus dihadapi oleh dunia pendidikan di bidang industri manufaktur khususnya bidang pemesinan di era Revolusi Industri 4.0 adalah meningkatkan kesiapan kerja agar memiliki kemampuan untuk menghasilkan produk pemesinan yang presisi, cepat dan murah dengan menggunakan mesin perkakas moderen.
Proses Manufaktur
Proses manufaktur merupakan suatu proses pembuatan benda kerja dari bahan baku sampai menjadi barang jadi atau setengah jadi dengan atau tanpa proses tambahan. Perkembangan proses manufaktur modern pada awalnya dimulai dari hasil eksperimen tentang pemotongan logam oleh Taylor pada tahun 1906. Hasil dari eksperimen tersebut selanjutnya menjadi dasar-dasar dari proses manufaktur. Proses manufaktur terutama yang berasal dari bahan logam dapat dikelompokkan sebagai berikut.
1. Proses pengecoran (casting, foundry or moulding processes)
2. Proses pembentukan (forming or metal working processes): rolling, forging, extrusion, drawing, and sheet metal work.
3. Proses Pemesinan (machining/metal cutting processes):
a. Conventional machining processes: turning, milling, drilling, shaping, grinding, dan broaching.
b. Nonconventional machining processes: Electro Chemical Machining (ECM), Electro Discharge Machining (EDM), Wire Electro Discharge Machining (WEDM), Abrasive Jet Machining (AJM), Ultrasonic Machining (USM), Liquid Jet Machining,
(LJM) Electron Beam Machining (EBM), Laser Beam Machining (LBM), Ion Beam Machining (IBM), dan Plasma Arc Machining (PAM).
4. Proses penyambungan (joining and assembly): welding, soldering, brazing, adhesive bonding, dan riveting.
5. Proses perlakuan fisik (heat treating): tempering, annealing, carburizing, dan hardening.
6. Proses pengerjaan akhir (Surface treatments/finishing): pelapisan dan pengecatan.
Dalam proses manufaktur, pembuatan suatu produk dapat dibuat dengan berbagai cara. Adapun pemilihan cara dalam pembuatan suatu produk tergantung pada jumlah produk, kualitas produk, fasilitas produksi yang tersedia, dan tuntutan standarisasi (Rahdiyanta, 2016). Jumlah produk yang dibuat akan mempengaruhi pemilihan proses pembuatan sebelum produksi dijalankan. Jumlah produk sangat berkaitan dengan pertimbangan dalam aspek ekonomis. Kualitas produk sangat ditentukan oleh fungsi dari komponen tersebut. Oleh sebab itu, kualitas produk yang akan dibuat harus mempertimbangkan kemampuan dari alat atau mesin yang tersedia. Fasilitas produksi yang tersedia dapat digunakan sebagai pertimbangan dalam aspek kualitas maupun kuantitas produksi yang akan dibuat. Penyeragaman (standarisasi), juga sangat berpengaruh terhadap pemilihan sistem manufaktur terutama pada produk yang harus mempunyai sifat mampu tukar (interchangeable). Standarisasi yang dimaksud meliputi bentuk geometri dan keadaan fisik dari suatu produk yang dibuat.
Proses Pemesinan
Proses pemesinan (machining process) merupakan proses manufaktur yang menghasilkan tatal (beram). Atau dengan kata lain proses pemesinan adalah merupakan suatu proses yang digunakan untuk menghilangkan sebagian dimensi dari benda kerja dengan mempergunakan mesin perkakas dan alat potong (metal cutting process) sehingga terbentuk komponen seperti yang dikehendaki (Amstead, 2009). Proses pemesinan hingga saat ini merupakan proses yang paling banyak digunakan (60% sampai dengan 80%) di dalam membuat suatu komponen-komponen mesin yang lengkap.
Dengan demikian, proses pemesinan merupakan proses manufaktur yang memiliki peranan sentral dalam pembuatan suatu unit peralatan atau mesin dengan menggunakan mesin perkakas.
Secara teknis proses pemesinan mulai dilakukan orang sejak diperkenalkan mesin koter (boring machine) oleh Wilkinson pada tahun 1775 yang digunakan untuk membuat komponen mesin-uapnya James Watt. Sekitar tahun 1794, Henry Maudslay membuat mesin bubut yang pertama. Pada tahun 1830, Joseph Withwort membuat alat ukur yang memiliki kecermatan sepersejuta inchi. Penemuan alat ukur tersebut amat sangat berharga, karena pada saat itu metode pengukuran yang cermat dibutuhkan untuk produksi massal komponen- komponen mesin yang mampu tukar (interchangeable parts). Sistem produksi massal sebenarnya baru diterapkan pada tahun 1798 yang dirancang oleh Whitney. Pada waktu itu ia menerima kontrak kerja dengan pemerintah Amerika Serikat untuk memproduksi senapan perang sebanyak 10.000 buah, dengan semua komponennya mampu tukar. Selama abad ke- 19, mesin perkakas standar seperti mesin bubut, frais, sekrap, planer, gerinda, gergaji, dan bor telah memiliki ketelitian yang cukup tinggi, dan memberikan dukungan yang sangat besar pada saat industrialisasi di Amerika Serikat dan Eropa dimulai. Sejak abad ke-20, mesin perkakas berkembang kemampuan produksinya dan menjadi semakin akurat.
Berkembangnya pemahaman tentang konsep mampu tukar (interchange-able) mengharuskan pengendalian dimensi produk secara ketat, sehingga proses perakitan dapat berjalan cepat dan biaya rendah. Oleh sebab itu, untuk mendukung pembuatan produk massal dalam proses pemesinan perlu dikembangkan jig dan fixtures. Jig dan fixtures pada dasarnya merupakan suatu alat bantu yang digunakan dalam proses pemesinan agar dapat menghasilkan duplikasi part yang lebih akurat (Hoffman, 1996). Fixture merupakan suatu alat bantu yang berfungsi untuk memposisikan, memegang, dan menahan benda kerja dalam proses produksi atau proses pemesinan. Sedangkan Jig berfungsi sebagai alat utama yang berperan untuk mengarahkan mata pahat (alat potong) pada benda kerja yang akan diproses sesuai dengan operasi yang diinginkan. Penggunaan jig dan fixture dalam proses pemesinan dapat menurunkan biaya manufaktur, menjaga kualitas, dan meningkatkan kapasitas produksi.
Klasifikasi proses pemesinan dapat dikelompokkan menjadi tiga yaitu berdasarkan: (1) jenis pahat (alat potong), (2) permukaan yang dihasilkan, dan (3) gerak relatif pahat terhadap benda kerja. Berdasarkan pahat yang digunakan, proses pemesinan dapat kelompokkan menjadi dua yaitu pahat bermata potong tunggal (single point cutting tool) dan pahat bermata potong jamak (multiple points cutting tool) (Kalpakjian, 2009). Sedangkan klasifikasi proses pemesinan berdasarkan permukaan yang dihasilkan juga dapat dikelompokkan menjadi dua, yaitu: (1) kelompok pertama adalah proses pemesinan untuk membentuk benda kerja silindris atau konis dengan benda kerja atau pahat berputar, dan (2) kelompok kedua adalah proses pemesinan untuk membentuk benda kerja permukaan datar dengan atau tanpa memutar benda kerja. Kelompok pertama meliputi proses bubut (turning/lathe), bor (drilling), frais (milling), gerinda datar (surface grinding), dan gerinda silindrik (cylindrical grinding). Sedangkan kelompok yang kedua meliputi proses sekrap (shaping/planing) serta proses gergaji dan parut (sawing and broaching).
Berdasarkan gerak relatif dari pahat terhadap benda kerja dapat dikelompokkan menjadi dua macam gerakan yaitu gerak potong (cutting movement) dan gerak makan (feeding movement). Pahat yang bergerak relatif terhadap benda kerja akan menghasilkan tatal dan sementara itu permukaan benda kerja secara bertahap akan terbentuk menjadi komponen yang dikehendaki.
Agar proses penyayatan logam dalam proses pemesinan dapatberlangsungsecaraefektif danefisien, perlumemperhatikan lima elemen dasar pemesinan yaitu: (1) kecepatan potong (cutting speed), (2) kecepatan makan (feeding speed ), (3) kedalaman potong (depth of cut), (4) waktu pemotongan (cutting time), dan (5) kecepatan penghasilan tatal (rate of metal removal). Elemen dasar pemesinan tersebut perlu ditetapkan berdasarkan dimensi benda kerja, pahat (alat potong), serta besaran dari mesin perkakas yang digunakan. Oleh sebab itu sangat penting untuk terus dilakukan berbagai penelitian mengenai proses pemesinan dengan tujuan seperti berikut.
a. Mengetahui mekanisme proses pemotongan logam dengan menggunakan pahat yang lebih optimal.
b. Mengetahui sifat kemudahan untuk dipotong (sifat ketermesinan) dari berbagai jenis logam yang relatif cepat perkembangannya.
c. Menemukan material/bahan yang digunakan sebagai pahat yang lebih baik sehingga menaikkan efisiensi pemesinan.
d. Mengetahui lebih jauh hubungan dari berbagai variabel proses pemotongan logam yang akan menjadi dasar pengembangan proses pemesinan yang optimum (Rochim, T. (1993).
Berbagai komponen mesin, hasil dari proses pemesinan dapat dilihat pada Gambar 3 berikut ini.
Gambar 3. Komponen Mesin Hasil dari Proses Pemesinan
Peranan Metrologi Industri dalam Proses Pemesinan
Untuk menjaga agar kualitas produk proses pemesinan tetap terkendali, perlu adanya dukungan fasilitas inspeksi atau kontrol kualitas yang memadai. Untuk memastikan bahwa produk yang dihasilkan memenuhi syarat baik dari segi dimensi geometris maupun kualitas permukaannya, perlu dilakukan pengukuran. Peranan metrologi industri yang terkait dengan pengukuran geometris suatu produk memegang peran yang sangat penting dalam proses pemesinan. Pengukuran geometris suatu produk harus dilakukan dengan cara dan alat yang tepat sehingga hasil pengukurannya mendekati kebenaran dari keadaan yang sesungguhnya (Munadi,1988). Dalam bidang teknik mesin ada beberapa istilah yang terkait dengan masalah pengukuran geometri suatu produk yaitu: ketelitian (precision), ketepatan (accuracy), ukuran dasar (basic size), toleransi (tolerance), harga batas (limits), dan kelonggaran (clearance).
Ketelitian (precision) adalah kesesuaian diantara beberapa data pengukuran yang sama yang dilakukan secara berulang. Tinggi rendahnya tingkat ketelitian hasil suatu pengukuran dapat dilihat dari harga deviasi hasil pengukuran. Perbedaan antara hasil pengukuran dengan ukuran dari benda ukur biasanya disebut dengan istilah kesalahan sistematis (systematic error). Semakin kecil kesalahan sistematis ini maka proses pengukuran yang dilakukan seseorang semakin teliti. Ketepatan (accurasy) adalah tingkat kedekatan dari nilai-nilai ukuran terhadap nilai yang sebenarnya. Apabila nilai–nilai ukuran semakin mendekati nilai sebenarnya, berarti penyimpangan atau kesalahan semakin kecil, maka berarti semakin tinggi akurasinya. Ukuran dasar (basic size) merupakan dimensi atau ukuran nominal dari suatu obyek ukur yang secara teoritis dianggap tidak mempunyai harga batas ataupun toleransi. Harga batas (limits) adalah ukuran atau dimensi maksimum dan minimum yang diizinkan dari suatu komponen, di atas dan di bawah ukuran dasar (basic size). Toleransi (tolerance) merupakan variasi atau perbedaan ukuran yang terletak di atas dan di bawah ukuran dasar (basic size).
Besarnya toleransi merupakan selisih dari ukuran maksimum dan ukuran minimum. Semakin presisi suatu komponen yang dibuat, maka besarnya toleransi juga makin kecil, sehingga proses pembuatan komponennya juga semakin kompleks. Hal ini berarti bahwa semakin kecil toleransi yang ditetapkan, akan berdampak pada biaya produksi yang harus dikeluarkan menjadi semakin besar, demikian pula sebaliknya. Kelonggaran (clearance) merupakan perbedaan ukuran antara pasangan suatu komponen dengan komponen lain di mana ukuran terbesar dari salah satu komponen adalah lebih kecil dari pada ukuran terkecil dari komponen yang lain. Sebagai contoh yang paling jelas misalnya pasangan antara poros dan lubang. Kelonggaran akan terjadi pada pasangan poros dan lubang tersebut apabila dimensi terluar dari poros lebih kecil dari pada dimensi terdalam dari lubang.
Geometris obyek ukur mempunyai bentuk dan ukuran yang bervariasi. Adanya variasi bentuk dan ukuran inilah yang menyebabkan timbulnya berbagai jenis alat ukur dan jenis pengukuran. Pengukuran adalah membandingkan suatu besaran dengan besaran standar. Syarat dari besaran standar yaitu dapat didefinisikan secara fisik, jelas dan tidak berubah terhadap waktu, dan dapat digunakan sebagai pembanding di semua tempat. Ada beberapa cara pengukuran yang dapat dilakukan untuk mengukur geometris obyek ukur yaitu:
1. Pengukuran Langsung
Proses pengukuran yang hasil pengukurannya dapat dibaca langsung dari alat ukur yang digunakan disebut dengan pengukuran langsung. Misalnya mengukur diameter poros dengan jangka sorong atau mikrometer.
2. Pengukuran Tak Langsung
Bila dalam proses pengukuran tidak bisa digunakan satu alat ukur saja dan tidak bisa dibaca langsung hasil pengukurannya maka pengukuran yang demikian ini disebut dengan pengukuran tak langsung. Misalnya mengukur ketirusan poros dengan menggunakan senter sinus (sine center) yang harus dibantu dengan jam ukur (dial indicator) dan blok ukur (gauge block).
3. Pengukuran dengan Kaliber Batas
Dengan menggunakan alat ukur jenis kaliber batas dapat ditentukan apakah benda yang dibuat masuk dalam kategori diterima (Go) atau masuk dalam kategori dibuang atau ditolak (No Go). Pengukuran cara ini tepat sekali untuk pengukuran dalam jumlah banyak dan membutuhkan waktu yang cepat.
4. Pengukuran dengan Bentuk Standar
Pengukuran sifatnya hanya membandingkan bentuk benda yang dibuat dengan bentuk standar yang digunakan sebagai alat pembanding. Sebagai contoh sudut ulir dicek dengan menggunakan mal ulir.
Menurut jenis dari benda yang akan diukur, alat ukur dapat pula diklasifikasikan sebagai berikut.
1. Alat ukur linier; baik alat ukur linier langsung maupun alat ukur linier tak langsung. Misalnya : pengukuran panjang, ketinggian, diameter, ketebalan, dan kedalaman.
2. Alat ukur sudut atau kemiringan. Ada alat ukur sudut yang langsung bisa dibaca skala sudutnya ada juga yang harus menggunakan perhitungan secara matematika, misalnya pada pengukuran bidang miring, taper, dan sudut.
3. Alat ukur kedataran, misalnya pengukuran straightness dan levelling.
4. Alat ukur profil atau bentuk, misalnya pengukuran foam dan kontur cetakan.
5. Alat ukur ulir, misalnya pengukuran pitch, diameter dalam, dan kedalaman ulir.
6. Alat ukur roda gigi, misalnya pengukuran modul roda gigi, tebal gigi, diameter pitch, dan tebal gigi.
7. Alat ukur untuk mengecek kekasaran permukaan, misalnya pengukuran flatness dan surface roughness.
Dengan demikian seorang operator mesin perkakas dituntut memiliki pengetahuan dan kemampuan dalam menggunakan berbagai alat ukur untuk memastikan bahwa produk yang dihasilkan benar-benar sesuai dengan gambar desain yang telah ditetapkan.
Keselamatan Kerja dalam Proses Pemesinan
Proses pemesinan merupakan salah satu proses manufakturing yang memiliki resiko tinggi terjadi kecelakaan kerja. Hal ini sangat beralasan karena dalam proses pemesinan melibatkan berbagai gerakan mekanis baik pada benda kerja, alat potong maupun bagian-bagian dari mesin perkakas itu sendiri. Oleh sebab itu Keselamatan dan Kesehatan kerja (K3) dalam proses pemesinan sangat penting untuk diperhatikan.
K3 mencakup semua aspek baik untuk manusia, mesin atau peralatan, benda kerja, dan lingkungan. Oleh sebab itu agar proses kerja di bidang pemesinan dapat berlangsung dengan baik maka perlu diperhatikan mengenai: manajemen K3, identifikasi penyebab timbulnya kecelakaan kerja, pengetahuan tindakan pencegahan kecelakaan kerja, pengetahuan tentang akibat dan penanggulangan kerja, dan pembudayaan K3 di bidang proses pemesinan (Rahdiyanta, 2019). Kondisi kerja yang tidak aman merupakan salah satu penyebab utama terjadinya kecelakaan dalam proses pemesinan. Sebagai contoh kondisi yang tidak aman dalam proses pemesinan adalah: (1) tidak menggunakan alat pelindung diri (APD), (2) peralatan yang tidak terlindungi secara benar, yaitu mesin dengan putaran tinggi tanpa diberi pelindung atau batas area, (3) peralatan yang rusak masih digunakan, (4) prosedur yang berbahaya, (5) cahaya yang tidak memadai, dan (6) ventilasi yang tidak sempurna.
CNC dan CAD/CAM sebagai Tuntutan di Era Revolusi Industri 4.0
Untuk memenuhi tuntutan produk pemesinan yang presisi, cepat, dan murah, telah dikembangkan mesin perkakas CNC yang dipadukan dengan perangkat lunak CAD/CAM. Mesin perkakas CNC (Computer Numerical Controlled) adalah mesin perkakas yang dalam pengoperasian proses pemotongan (cutting) benda kerja oleh pahat atau alat potong, dibantu dengan control numeric dengan menggunakan komputer. CAD/CAM adalah singkatan dari Computer Aided Design and Computer Aided Manufacturing. CAD (Computer Aided Design) adalah program komputer yang memungkinkan seorang perancang (designer) untuk mendesain gambar rekayasa (design engineering) dengan mentransformasikan gambar geometris secara cepat dan presisi. Sedangkan CAM (Computer Aided Manufacturing) adalah sistem manufaktur yang mengoptimalkan kemampuan program komputer untuk menterjemahkan desain rekayasa yang dibuat oleh CAD sehingga dapat mengontrol mesin CNC. Sistem CAD/CAM sendiri terjadi apabila spesifikasi desain secara langsung ditransfer/ diterjemahkan kedalam spesifikasi manufaktur. Dengan demikian CAD/CAM merupakan penggabungan desain rekayasa dan instruksi manufaktur. Sedangkan mesin CNC sendiri adalah mesin yang peralatannya dikontrol oleh komputer dengan sistem CAD/CAM.
CAD/CAM mempunyai fungsi utama dalam desain, analisa, optimasi dan manufaktur. Dalam perkembangan lebih lanjut CAD/CAM dapat digunakan untuk melakukan analisa elemen hingga (finite element analysis), analisa transfer panas (heat transfer analysis), analisa tekanan (stress analysis), simulasi dinamis dari mekanik (dynamic simulation of mechanisms), dan analisa cairan dinamis (fluid dynamic analysis). Kemampuan CAD/CAM pada dasarnya terdiri dari empat teknologi dasar yaitu: (1) manajemen basis data (database), (2) komputer grafik, (3) model matematis (analysis), dan (4) akuisisi data kontrol (prototipe fisik dan proses produksi). Manfaat dan keunggulan dari penggunaan CAD/CAM dalam proses pemesinan adalah: (1) dapat merespon kebutuhan secara cepat dan akurat, (2) desain manufaktur yang lebih fleksibel, (3) meningkatkan mutu produk, (4) menurunkan biaya produksi per unit, dan (4) mengurangi kebutuhan untuk membuat prototipe fisik (Peter, 2012).
Dalam perkembangannya terdapat banyak perangkat lunak CAD/CAM yang dapat digunakan dalam proses pemesinan pada saat ini, antara lain: Emcodraft CAD/CAM, MasterCam, BobCam, DelCam, dan SolidCam. Proses pemesinan pada saat ini banyak menggunakan perangkat lunak Mastercam. Perangkat lunak Mastercam adalah perangkat lunak yang dikembangkan oleh CNC Software, Inc. dari Amerika Serikat. Mastercam adalah perangkat lunak yang digunakan untuk menggambar (design) dan membuat program CNC pada mesin bubut, frais maupun wire cutting. Pengetahuan atau kemampuan yang harus dikuasai untuk dapat menggunakan perangkat lunak mastercam ini adalah: (1) kemampuan mengoperasikan komputer dengan sistem operasi windows, (2) kemampuan membaca gambar kerja, dan (3) menguasai teori dan praktik proses pemesinan bubut CNC dan frais CNC (Wijanarka, 2012).
Kompetensi yang harus dikuasai agar dapat menggunakan mesin CNC dan CAD/CAM secara terpadu dalam proses pemesinan meliputi: (1) menggambar bentuk 2D dan 3D dengan fasilitas CAD, (2) menyusun program CNC berdasarkan CAD (baik 2D/3D) dengan menggunakan CAM, (3) kemampuan memilih alat potong sesuai dengan jenis pekerjaan, (4) kemampuan menentukan lintasan alat potong (urutan kerja), (5) kemampuan melakukan simulasi program CNC, (6) pengoperasian mesin CNC untuk pengerjaan benda kerja, dan (7) kemampuan melakukan pengukuran menggunakan alat ukur presisi (Rahdiyanta, 2019).
Pembelajaran Pemesinan di Era Revolusi Industri 4.0
Di era Revolusi Industri 4.0, setiap bangsa dituntut untuk menyiapkan sumber daya manusia dalam penguasaan teknologi- teknologi kunci seperti teknologi sensor dan robotic, internet of think (IoT) dan komputasi awan, analisis data raksasa, dan jaringan pabrik (Jeevita and Ramya, 2019). Oleh sebab itu pembelajaran di era Revolusi Industri 4.0 harus didorong menjadi pembelajaran yang dicirikan dengan smartization dan produksi inovasi di segala bidang dengan mengoptimalkan teknologi informasi terkini. Perkembangan teknologi digital dalam proses pembelajaran semakin mudah diakses melalui gawai (smartphone). Hampir semua gawai dapat digunakan untuk mengakses sumber-sumber pembelajaran online learning melalui massive open online courses (MOOCs) dan blended learning. Oleh sebab itu pembelajaran pada RI 4.0 secara umum perlu difokuskan pada usaha-usaha:
1. membekali lulusan dengan pengetahuan dan kemampuan bekerja untuk menghadapi tantangan dunia kerja masa depan dan memiliki sikap, karakter, integritas, dan nilai-nilai ke- indonesia-an yang kuat;
2. mendorong peserta didik untuk menggunakan sumber-sumber belajar internal dan eksternal dengan memanfaatkan teknologi informasi;
3. menggunakan kompetensi abad ke-21, yaitu collaboration, communication, creativity and critical thinking;
4. mendorong pembelajaran sepanjang hayat (lifelong learnig) sebagai salah satu target program education 2030 yang ditetapkan dalam sustainable development goals); dan
5. menghasilkan pengetahuan, teknologi, seni, dan inovasi- inovasi baru.
Tujuan dari pembelajaran pemesinan ditekankan pada pencapaian kompetensi dalam dua hal, yaitu proses kerja dan hasil kerja (produk). Proses kerja meliputi: langkah kerja, penggunaan mesin dan alat bantu, penggunaan alat ukur, perawatan mesin dan alat bantu, alokasi waktu yang digunakan, sikap kerja, dan keselamatan kerja. Sedangkan hasil kerja yang berupa produk, ditekankan pada kualitas dimensi, kualitas geometri, dan kualitas permukaan benda kerja atau tingkat kekasarannya (Rahdiyanta, 2017). Agar pembelajaran proses pemesinan dapat berjalan dengan baik, peserta didik harus memiliki kemampuan pendukung di bidang: (1) gambar teknik, (2) ilmu bahan, (3) metrologi industri, dan (4) teori pemesinan.
Tantangan dalam pembelajaran pemesinan moderen adalah masalah ketersediaan fasilitas mesin CNC dan CAD/ CAM di dunia pendidikan. Fasilitas mesin CNC dan CAD/ CAM di kampus/sekolah masih dirasa sangat kurang dan masih tertinggal dengan yang ada di industri. Hal ini mengakibatkan link and match antara lembaga pendidikan dengan dunia industri bermasalah (Wijanarka, 2018). Untuk mengatasi tantangan tersebut dan sekaligus untuk meningkatkan kesiapan kerja siswa di bidang pemesinan perlu dikembangkan model pembelajaran yang melibatkan secara langsung dunia industri atau dunia kerja (Rahdiyanta, 2019). Kerja sama dengan dunia industri sangat penting dilakukan karena dua pertimbangan yaitu : (1) mesin CNC dan CAD/CAM mahal harganya, dan (2) pihak industri lebih menguasai teknologi maju. Salah satu model pembelajaran yang cocok digunakan adalah model pembelajaran teaching industry. Teaching industry adalah wahana produktif berbasis riset/ penelitian dan inovasi untuk mendukung proses pembelajaran yang bersinergi dengan industri dan pemerintah. Perguruan tinggi memanfaatkan teaching industry sebagai wahana untuk hilirisasi/pembuatan produk-produk hasil penelitiannya dan melatih para mahasiswa melakukan praktik real melalui praktik kerja industri atau pembelajaran di tempat kerja (Work Based Learning). Industri dapat memanfaatkan teaching industry untuk memproduksi barang atau suku cadang yang diperlukan untuk kelengkapan produknya. Pada teaching industry, sumber daya pembelajaran (dosen/guru, laboratorium, dan pustaka) yang ada di kampus dapat dimanfaatkan untuk peningkatan skills dan kompetensi sumber daya manusia untuk penciptaan nilai tambah dan peningkatan produktivitas. Dari model pembelajaran teaching industry di bidang pemesinan ini diharapkan akan muncul produk-produk penghiliran hasil riset dan inovasi perguruan tinggi yang diharapkan dapat masuk ke segmen pasar sebagai substitusi produk-produk impor, sehingga ketergantungan Indonesia terhadap produk impor khususnya dibidang komponen-komponen mesin dapat berkurang secara bertahap. Oleh sebab itu baik perguruan tinggi maupun Sekolah Menengah Kejuruan (SMK) perlu segera mengimplementasikan model pembelajaran teaching industry.
Agar implementasi pembelajaran teaching industry dapat berjalan dengan baik perlu dilakukan kerja sama yang sinergis yang melibatkan pihak manajemen baik di kampus maupun industri, alumni, profesional, praktisi industri, dan ahli pembelajaran dengan tujuan untuk menginspirasi dan memfasilitasi proses perolehan pengalaman nyata di industri pemesinan. Dengan model pembelajaran teaching industry diharapkan para siswa/ mahasiswa memiliki kemampuan: (1) berkomunikasi lisan dan tertulis terkait dengan proses manufaktur di bidang pemesinan, (2) memproyeksikan diri di bidang proses pemesinan, (3) menyusun perencanaan dalam pembuatan produk di bidang pemesinan, (4) membuat keputusan strategis di bidang pemesinan, (5) memiliki etika kerja di bidang pemesinan, dan (6) menjadi problem solver yang berjiwa social entrepreneurial di bidang manufaktur (Rahdiyanta, 2019). Agar pelaksanaan teaching industry dalam pembelajaran pemesinan dapat berlangsung secara efektif dan efisien, guru/ dosen perlu menggunakan blended learning dengan menggunakan perpaduan fasilitas belajar online, tatap muka dan memberi pengalaman belajar langsung melalui proses penelitian.
Lebih lanjut dalam upaya mewujudkan Konsep Pendidikan 4.0, perlu segera mengembangkan strategi Ekosistem Pendidikan Inovatif di bidang pemesinan yang meliputi:
1. Implementasi Outcome Based Education (OBE) dalam kurikulum khususnya yang terkait dengan bidang pemesinan.
Dalam pembelajaran proses pemesinan, OBE dilaksanakan secara bertahap melalui Problem Based Learning, dan Project Based Learning, dan pada tahap akhir melaksanakan Production Based Learning.
2. Pengembangan metode dan konsep pembelajaran yang meliputi yang meliputi:
a. Penguatan metode student centered learning.
b. Optimalisasi pemanfaatan teknologi informasi melalui implementasi blended learning di bidang pemesinan.
c. Pengembangan konten-konten pembelajaran berbasis visual (visual-based-learning) di bidang pemesinan (Rahdiyanta, 2020).
d. Diseminasi pengetahuan proses pemesinan melalui kanal- kanal pengetahuan di universitas/sekolah.
3. Penyediaan fasilitas learning space dan coworking space yang memadai untuk mendukung pembelajaran proses pemesinan.
Di era Revolusi Industri 4.0, guru/dosen menghadapi tantangan dalam proses pembelajaran. Tantangan tersebut berasal dari perkembangan teknologi digital di bidang informasi dan komunikasi yang memberi dampak pada teknologi pembelajaran dan perubahan karakter peserta didik dalam belajar. Tantangan real yang dihadapi para guru adalah bahwa para siswa telah mengenal teknologi informasi dan komunikasi (TIK) dalam usia yang lebih dini dari pada gurunya. Bahkan pada beberapa hal tertentu, kemungkinan siswa akan lebih unggul dan lebih cepat belajar TIK dari pada gurunya. Douglas Rushkoff (2014) menyatakan bahwa: Children are native to cyberspace, and we, as adults, are immigrants.” Hal ini tidak mengherankan karena anak-anak sekarang (millenial), sejak kecil sudah dikenalkan dengan komputer dan dunia maya, sedangkan orang yang telah dewasa adalah pendatang baru pada dunia maya. Generasi muda (millennial) saat ini telah menjadi net generation/I Genertion. Lingkungan bermain generasi ini lebih banyak berinteraksi dengan media interaktif on line. Kebiasaan mereka menggunakan fasilitas internet menuntut guru untuk mengajar dengan cara yang berbeda. Apabila proses pembelajaran kurang menarik, perhatian siswa menjadi berkurang, karena siswa merasa dapat belajar lebih cepat dan lebih mudah dengan caranya sendiri menggunakan internet.
Untuk mengatasi masalah tersebut para guru/dosen dituntut dapat melaksanakan pembelajaran menggunakan multi user virtual environments (MUVEs). Agar dapat melaksanakan pembelajaran menggunakan MUVEs dengan baik, para guru/dosen harus menguasai kemampuan yang terkait dengan: (1) Data Literacy, yaitu kemampuan untuk membaca, menganalisis, dan menggunakan Big Data (informasi) di dunia digital; (2) Technological Literacy, yaitu meliputi: coding, artificial intelligence, dan engineering principles (memahami cara kerja mesin, dan aplikasi teknologi); dan (3) Human Literacy (humanities, communication, dan design).
Revolusi Industri 4.0 sudah hadir. Salah satu cara untuk menyambutnya adalah dengan meningkatkan kualitas pendidikan. Pendidikan merupakan investasi masa depan dengan guru/dosen sebagai garda terdepannya. Oleh sebab itu, guru/dosen harus memilik karakter yang mulia, pandai dalam mengkomunikasikan materi pelajaran, bisa melakukan pendekatan analisis dan sintesis, dinamis dan antusias, serta dapat melakukan interaksi dengan baik.
Sumber:
Pidato Pengukuhan Prof. Dr. Ir. Dwi Rahdiyanta, M.Pd. sebagai Guru Besar dalam Bidang Ilmu Pembelajaran Proses Pemesinan pada Fakultas Teknik Universitas Negeri Yogyakarta, dengan judul “Tantangan Pembelajaran Pemesinan Di Era Revolusi Industri 4.0”, Sabtu, 15 Februari 2020
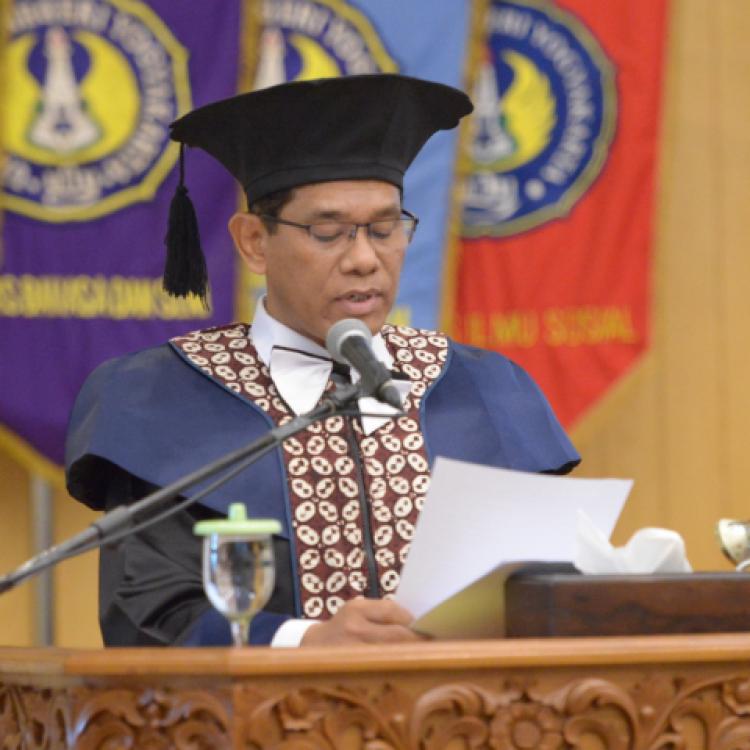